Inquire
INDUSTRIAL IoT(IIoT) WITH PREDICTIVE MAINTENANCE
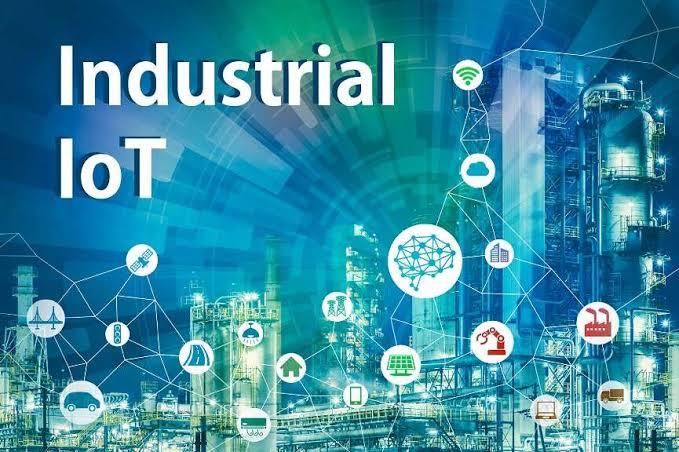
Industrial Internet of Things (IIoT) refers to the integration of intelligent sensors, embedded systems, and networked devices in industrial environments to enable automation, data exchange, and advanced analytics. Predictive Maintenance (PdM) is a key application of IIoT, which uses sensor data and machine learning algorithms to forecast equipment failures and optimize maintenance schedules, thus enhancing operational efficiency and minimizing unplanned downtime.
System Overview:
The IIoT-based predictive maintenance system is built upon five key layers:
1. Sensor Layer (Data Acquisition):
Various industrial-grade sensors are deployed on critical machinery components:
Accelerometers (e.g., ADXL335) – for vibration analysis
Thermocouples or RTDs (e.g., PT100) – for temperature measurement
Current sensors (e.g., ACS712) – to monitor electrical consumption
Humidity and pressure sensors – to detect environmental conditions
These sensors generate real-time data representing the health of machinery.
2. Edge Computing Layer:
An edge device such as a Raspberry Pi, ESP32, or Industrial Gateway collects and preprocesses sensor data. Signal conditioning, data filtering, and threshold-based anomaly detection are performed locally to reduce data latency and bandwidth consumption.
3. Communication Layer:
Data is transmitted to the cloud via:
Protocols: MQTT (Message Queuing Telemetry Transport), HTTP, or CoAP
Networks: Wi-Fi, Ethernet, LoRaWAN, or 5G NR
MQTT is commonly used for lightweight, low-latency communication in industrial networks.
4. Cloud and Analytics Layer:
Cloud platforms like AWS IoT Core, Microsoft Azure IoT Hub, or Google Cloud IoT store and process sensor data. The predictive maintenance engine uses:
Time-Series Databases (e.g., InfluxDB)
ML Models (Regression, SVM, LSTM) to predict Remaining Useful Life (RUL)
Anomaly Detection Algorithms to identify early signs of machine failure
5. Application Layer (User Interface):
A dashboard built using tools like Grafana, Power BI, or Node-RED allows operators to:
View real-time equipment condition
Track predictive alerts
Access historical data trends
Receive notifications (via SMS/Email/App)
Real-Time Use Case Example:
In a manufacturing plant, a CNC machine is instrumented with a vibration sensor. Over time, the ML model identifies abnormal frequency patterns. The system predicts a possible spindle bearing failure in 48 hours. An automated alert is sent, and maintenance is scheduled in advance—thus preventing unexpected downtime and saving maintenance costs.
Conclusion:
Industrial IoT with Predictive Maintenance revolutionizes traditional maintenance strategies by shifting from reactive or scheduled servicing to data-driven proactive care. By leveraging real-time sensor data, edge processing, secure communication protocols, cloud-based analytics, and AI models, IIoT enhances equipment reliability, reduces maintenance overheads, and contributes to the core objectives of Industry 4.0: automation, smart monitoring, and sustainable production.
- Managerial Effectiveness!
- Future and Predictions
- Motivatinal / Inspiring
- Other
- Entrepreneurship
- Mentoring & Guidance
- Marketing
- Networking
- HR & Recruiting
- Literature
- Shopping
- Career Management & Advancement